As more Sydney homeowners aim for energy-efficient, comfortable homes, standards like Passive House (or PassivHaus) are becoming increasingly popular, especially in renovations and modern granny flat builds. Rising energy costs, climate concerns, and better building awareness are all driving this shift toward high-performance design. One of the most important and overlooked factors in these builds is airtightness. Airtightness depends on skilled detailing at every junction, chase, and corner, and that’s where a plasterer becomes critical. To understand why it matters, let’s take a closer look at what Passive House really means and how airtightness fits in.
What Is Passive House and Why Airtightness Matters
Passive House or PassivHaus is a globally recognised building standard designed to drastically reduce the need for heating and cooling while delivering consistent indoor comfort and better air quality. The Australian Passivhaus Association outlines its five core principles: super insulated envelopes, airtight construction, thermal bridge-free design, high-performance windows, and mechanical ventilation with heat recovery (MVHR). These work together to create a home that stays warm in winter, cool in summer, and costs far less to run.
Among the principles, airtightness often goes unnoticed, but it’s absolutely essential. Without it, air leaks compromise the performance of even the best insulation or glazing. Airtightness prevents heat from escaping in winter, blocks unwanted hot air in summer, and ensures your MVHR system provides clean, filtered air without energy loss. It also reduces noise, dampness, and allergens, which is an added bonus for urban Sydney homes.
This is important for older houses across Sydney. Many homes were built before airtightness was considered, so gaps, cracks, and poor sealing are common. When retrofitting to a Passive House or high-performance standards, improving airtightness is often the most powerful step in boosting comfort and cutting long-term energy bills.
Airtightness Isn’t Just About Membranes: The Plasterer’s Role
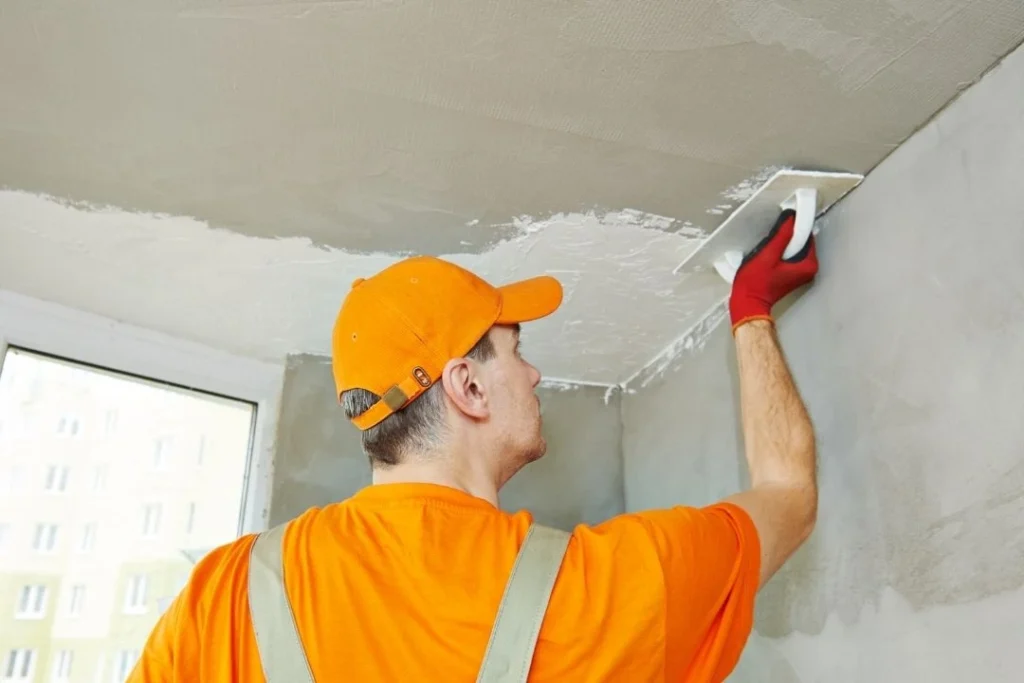
When people think of airtight construction, they often picture building wraps, membranes, and flashing tapes. While those elements do help form the airtight layer, they’re only part of the picture. Airtightness isn’t achieved through materials alone. It’s built through precision, and that’s where the plasterer plays an important role.
In many homes, especially retrofits, the internal plaster layer ends up being the most continuous and robust air barrier. A skilled plasterer seals up weak points in your building envelope, aside from smoothing out walls. By carefully detailing plasterboard junctions, service chases, and tricky corners, they create a seamless internal layer that blocks air leakage and helps the whole system perform.
Key areas a plasterer must seal include:
- Plasterboard joints and internal corners
- Ceiling-to-wall connections, including bulkheads and shadowlines
- Electrical boxes, plumbing chases, and service penetrations
- Downlights and recessed lighting points
Membranes may handle the external side of things, but inside the home, it’s the plastering that holds it all together. If you want to hit Passive House standards or just want a more comfortable, energy-efficient Sydney home, your plasterer needs to be part of the airtightness strategy.
Plastering Techniques That Improve Airtightness
Airtight performance matters as much as the aesthetics when plastering for a Passive House build. Every joint, corner, and service penetration must be sealed with precision, using specialised techniques that directly contribute to the home’s airtight envelope. Here’s how a skilled plasterer makes that airtight layer durable without compromising the finish:
- Air-tight jointing compounds are applied with care, reinforced with mesh tape at vulnerable junctions to prevent cracks or air leaks.
- PVA primers are used on porous surfaces to improve adhesion and durability over time.
- Service penetrations like electrical boxes, conduits, or plumbing chases are sealed using plaster or air-tight sleeves before the final coat is applied.
- Close coordination with the builder or air-sealing contractor ensures that plastering integrates seamlessly with membranes, tapes, and other airtight layers.
- On some builds, a continuous skim coat is used across the entire internal walls to serve as the primary internal air barrier.
Common Mistakes in Airtightness During Plastering

Even the best materials can fall short if airtightness isn’t treated as part of the plastering process. Small errors can lead to major air leaks that compromise the entire system. Here are some common airtightness mistakes to watch out for:
- Over-sanding joint compounds can create microgaps at seams and junctions.
- Leaving service penetrations unsealed, especially around pipes, conduits, or electrical boxes.
- Poor coordination with other trades, leading to missed sealing opportunities once walls are closed.
- Using standard jointing products, instead of airtight-specific systems built for Passive House or high-performance standards.
- Neglecting tricky areas like downlights, bulkheads, or shadowlines, where small gaps can result in significant leakage.
In high-performance construction, airtightness demands precision. That’s why it’s critical to work with trained, detail-focused Sydney plasterers who understand how their work fits into the bigger airtightness strategy. Without attention to detail, even a well-insulated home can fall short on comfort and energy efficiency.
How Airtight Plastering Improves Sydney Retrofits and Granny Flats
Sydney homes are often older and naturally draughty, built before airtightness was a design priority. Brick veneers, fibro cottages, and timber frames typically have gaps and cracks that allow heat to escape and outside air to creep in. When retrofitting for energy efficiency, airtight plastering can make a dramatic difference in comfort and performance. Combined with proper insulation, it forms the foundation of a high-performing building envelope, helping improve comfort and reduce energy bills in Sydney homes.
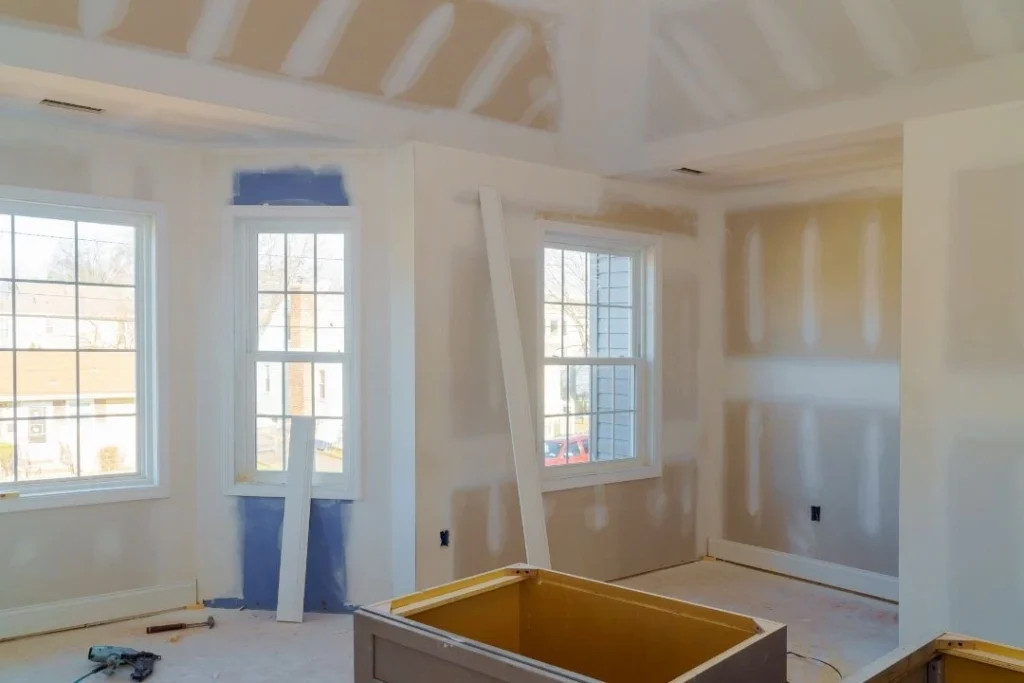
By sealing internal corners, junctions, and service penetrations, trained plasterers can help transform leaky homes into more stable, energy-efficient spaces. Airtight plastering doesn’t rely on moving parts, high-tech systems, or ongoing maintenance. It’s a passive solution that delivers long-term results.
Granny flats built to Passive House or similar standards also benefit from this precision. Because these smaller structures have tighter tolerances, every trade needs to deliver airtight results to maintain compliance, and plastering is a critical part of it. With the right detailing, you get a compact home that’s quieter, easier to heat or cool, and built for long-term comfort.
Work with a Plasterer Who Understands Passive House
Whether you’re retrofitting a draughty Sydney home or building a new high-performance granny flat, or new build airtight plastering is one of the most effective, low-maintenance ways to improve thermal comfort and energy efficiency. It doesn’t rely on mechanical parts, and once it’s done right, it stays sealed for the long haul. Airtightness can’t be added on at the end. It has to be built into the home from the inside out.
That’s why it’s so important to work with a plasterer who understands Passive House standards, detail coordination, and the real science behind airtight design. We help create airtight building envelopes that support your comfort, sustainability goals, and blower door test success. From sealing service penetrations to coordinating with builders on high-performance projects, we bring the detail-focused approach that Passive House builds demand.
If you’re planning a Passive House retrofit or energy-efficient build in Sydney, reach out to us. We’ll help you seal the deal—literally.